As I mentioned on Monday last October, I went to Huddersfield, England, to visit Marling and Evans, a 270-year-old mill and one of the last remaining in the region. My aim was to learn how cloth is made. If you haven't seen that video, you can click here.
Before this trip, I had incorrectly assumed that the mill was the final part of the cloth-making process. I had no idea there was another equally important part—the finisher.
My journey to Huddersfield led me to W.T. Johnson & Sons, one of England's last finishers. Established in 1910, this renowned textile finishing company has been a cornerstone of Huddersfield's textile industry for over a century, and it remains proud to be in operation today. I got a facility tour from Allen, who had run the finisher for several decades. What started as a small family-operated business has grown into one of Yorkshire's premier textile finishing facilities, a testament to this region's enduring legacy of textile craftsmanship.
The textile finisher's role is simple: take the raw cloth from the mill and treat it to prepare it to withstand the demands of everyday wear.
I'm sure you all have felt a very dense, scratchy wool jacket—that roughness directly results from the finisher. As it turns out, that same material could also be finished smoothly. It's all based on the desired outcome from the mill and the machinery in the finisher. Different jackets call for different finishing. In addition, as I learned, cloth can be treated with a different level of 'sheen.' Mark, who runs Marling and Evans, was telling me.
Just as New Yorkers credit their delicious pizza to the city's unique water, the locals in Huddersfield attribute their area's once-highest cloth production in the world to the same element. 'The water' here played a significant role, they say, in creating the perfect conditions for treating the fabric and finishing it in a beautiful and enduring way.
Operating from its facility in Huddersfield, W.T. Johnson developed a reputation for excellence in finishing delicate worsted fabrics. Its specialized techniques in decreasing and shrinking processes became particularly sought after by luxury cloth manufacturers. The company's expertise in finishing delicate fabrics, especially those destined for high-end tailoring, helped maintain Huddersfield's status as a global center for premium textile production.
Water was so essential to their process that in the 1930s, they wanted to drill underneath the finishers and build their own well to get water directly from the ground beneath them. They had to drill thousands of feet, but they found it.
Despite the overall decline of the British textile industry in the latter half of the 20th century, W.T. Johnson & Sons continued to thrive. As any good business does, when they start to make significant profits, they reinvest it into the company. They built the well to source their own water, upgraded to the latest machinery, and provided an assortment of finishes for their customers. I learned that these machines aren't cheap. This reinvestment is undoubtedly why they are still operating today, while many of their competitors have long since closed down.
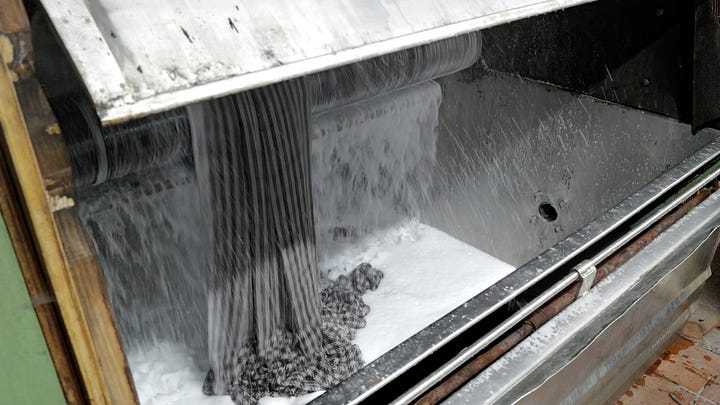
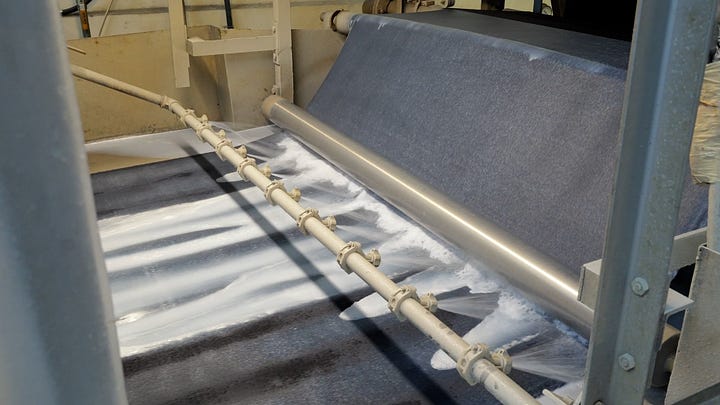
The finishing process begins with scouring, a crucial preliminary treatment that removes natural impurities, oils, waxes, and dirt from the fabric. Textiles are treated with alkaline solutions during scouring, typically sodium hydroxide or sodium carbonate, combined with specialized detergents and surfactants. This process is carried out at elevated temperatures, usually between 50°C and 100°C, depending on the fiber type. The thorough cleaning achieved through scouring creates an optimal foundation for subsequent finishing processes.
After scouring, finishers employ chemical and mechanical processes to enhance the fabric's properties. Chemical finishing involves applying various treatments to impart specific characteristics such as water resistance, flame resistance, or softness. Mechanical finishing includes processes like calendering (pressing between rollers), raising (creating a soft surface), and stentering (maintaining width and straightness).
Mark from Marling and Evans says this process ensures that when you take your blazer to the dry cleaners, your jacket doesn't go from a 40 to a 36.
Like Marling and Evans, W.T. Johnsons is one of the last remaining finishers in the area, and it's retained its position because of the quality of work they produce. Watch my latest video, How Cloth is Made, to learn more about this process. It was an incredible honor to be able to visit both Marling and Evans and W.T. Johnson on the same day, to meet Mark and Allen who run the companies, two legends in their fields, and to be able to shed some light on this incredible process.